In the realm of material processing and industrial applications, ball mills stand as stalwart workhorses, facilitating the grinding, blending, and homogenization of various substances. Their versatile nature and efficient operation have made them indispensable tools across a spectrum of industries, from mining and ceramics to pharmaceuticals and beyond. In this article, we delve into the essence of ball mills, unraveling their mechanics, applications, and significance in modern manufacturing processes.
Understanding the Mechanics of Ball Mills
A ball mill represents a cylindrical device employed for grinding, blending, and homogenizing materials. Its design encompasses a hollow cylindrical shell, typically made of steel, rotating around its axis. Within this shell, various materials are introduced, typically in the form of granules or powders, along with grinding media—spherical balls made of steel, ceramic, or other materials.
The primary mechanism driving ball mill operation is based on the principles of impact and attrition. As the mill rotates, the grinding media within it (the balls) are lifted to a certain height and then free-fall, impacting the material to be ground. This repeated impact between the grinding media and the material results in size reduction through fragmentation and abrasion.
Types of Ball Mills
Ball mills come in various configurations tailored to suit different applications and processing requirements. Some common types include:
Overflow Ball Mills: These mills feature a grate discharge design, allowing for the discharge of ground material through the grate slots at the periphery of the mill. They are suitable for wet grinding operations and are commonly used in mineral processing applications.
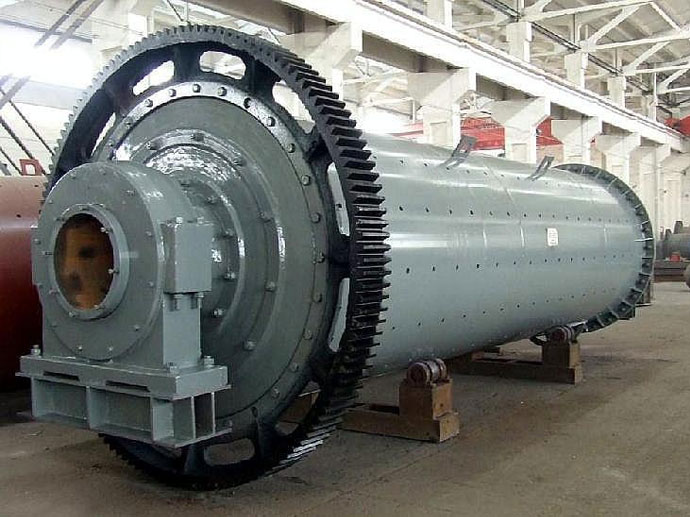
Grate Discharge Ball Mills: In contrast to overflow mills, grate discharge ball mills have a discharge diaphragm at the outlet, controlling the material flow and ensuring efficient grinding. These mills are often employed in the cement industry.
Batch Ball Mills: Batch mills are designed for intermittent operation, typically used in laboratory settings or small-scale production environments. They allow for precise control over the grinding process and are well-suited for grinding small quantities of materials.
Continuous Ball Mills: Continuous mills operate continuously, allowing for continuous feed and discharge of material. They are employed in large-scale industrial processes requiring continuous grinding operations.
Applications of Ball Mills
The versatility of ball mills lends them to a wide array of applications across diverse industries. Some key applications include:
Mineral Processing: Ball mills are extensively used in mineral processing plants for grinding ores and other materials. They play a crucial role in comminution processes, facilitating the extraction of valuable minerals from ore bodies.
Ceramics: In the ceramics industry, ball mills are utilized for grinding raw materials and preparing ceramic powders for forming processes such as molding and extrusion.
Pharmaceuticals: Ball mills find applications in pharmaceutical manufacturing for grinding and homogenizing active pharmaceutical ingredients (APIs) and excipients. They are integral to processes such as drug formulation and particle size reduction.
Paints and Pigments: Ball mills are employed in the production of paints, pigments, and coatings, where they facilitate the dispersion of pigments within the liquid medium, ensuring uniform coloration and quality.
Chemical Processing: Ball mills are used in various chemical processing applications, including grinding and blending of chemicals, production of specialty chemicals, and synthesis of materials.
Significance of Ball Mills in Modern Manufacturing
The significance of ball mills in modern manufacturing processes cannot be overstated. Their ability to efficiently grind, blend, and homogenize materials plays a crucial role in ensuring product quality, process efficiency, and cost-effectiveness. Some key aspects of their significance include:
Size Reduction: Ball mills enable size reduction of materials to achieve desired particle sizes, critical for downstream processes such as mixing, granulation, and formulation.
Process Control: Ball mills offer precise control over the grinding process, allowing for adjustments in parameters such as rotation speed, grinding media size, and material feed rate to achieve desired outcomes.
Product Quality: The uniformity and consistency of product particle size and distribution achieved through ball milling contribute to the overall quality and performance of manufactured products.
Versatility: The versatility of ball mills makes them suitable for a wide range of applications across diverse industries, from heavy-duty industrial processes to laboratory-scale research and development.
In conclusion, ball mills represent indispensable tools in modern manufacturing processes, serving as versatile and efficient means for grinding, blending, and homogenizing materials. Their robust design, coupled with precise control over process parameters, ensures consistent performance and high product quality across a spectrum of industries. As technology advances and manufacturing requirements evolve, the role of ball mills is likely to remain central to material processing and industrial applications, driving innovation and progress in diverse fields.