Hammer mill is a versatile machine widely used in various industries for crushing and grinding different materials. However, the inherent nature of its operation creates potential safety risks for operators and maintenance personnel. Recognizing the importance of worker safety, manufacturers and industry stakeholders have been actively working to integrate improved safety features into hammer mills. This article explores the advances in safety measures adopted by hammer crushers to create a safer working environment for those involved in their operation and maintenance.
Learn about hammer mills
Before delving into safety features, it is necessary to have a basic understanding of how a hammer crusher works. These machines consist of a rotating shaft equipped with a freely swinging hammer. The material to be processed is fed into the mill, where a hammer driven by an electric motor or other power source impacts the material and breaks it down into smaller particles. While effective in reducing size, the hammer's high-speed rotation and powerful impact pose inherent safety challenges.
Common safety issues with hammer mills
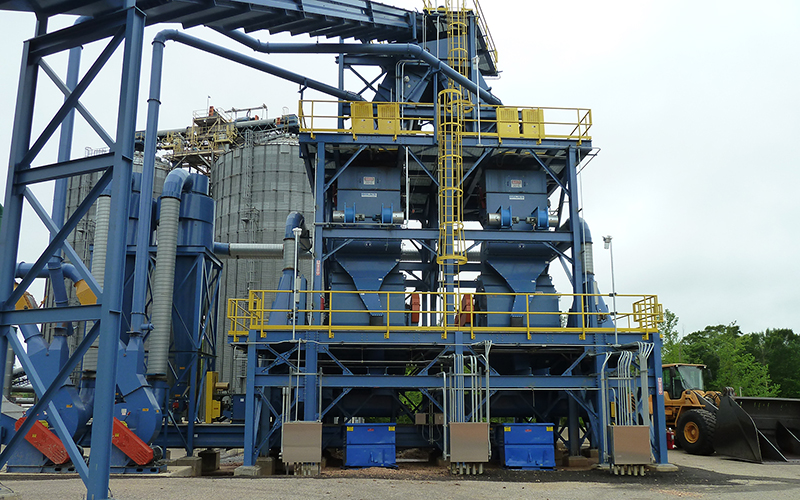
High speed rotation:
When the machine is working, the rapid rotation of the hammer will bring a certain risk of injury to workers at close range and routine maintenance personnel, especially during maintenance or when the operator is close to the machine. Strictly abide by the requirements of safety regulations, maintain a safe distance, abide by operating specifications, and never take risks when the machine is running to prevent the occurrence of danger.
Dust and particulate emissions:
During the processing of materials in a hammer mill, a large amount of dust and particles will be produced, causing harm to the respiratory system and the environment. At this point, local environmental protection departments must have corresponding requirements and standards. During our production process, we must control dust particle emissions and comply with the requirements of the environmental protection department. Many green mining projects now use indoor production and spray systems to effectively reduce dust. When necessary, air purification equipment needs to be purchased to reduce dust emissions.
Interference and blocking:
The material in the hammer mill occasionally becomes clogged during operation, or the blockage may cause the stored energy to be suddenly released, causing potential danger to the operator. Therefore, when a blockage occurs, corresponding measures must be taken promptly according to the operation manual. Avoid personal injury and equipment damage.
Electrical hazards:
Equipment requires electrical energy to operate. Electrical components and wiring in a hammer crusher can cause electric shock or fire if power supply equipment and wiring are not adequately protected. Therefore, attention should be paid to the aging of power supply system equipment and lines during daily maintenance. Put an end to working while sick and prevent losses caused by electricity from the root cause.
Innovations that improve safety
Safety interlocks and sensors:
Modern hammer mills are equipped with safety interlocks and sensors to detect and respond to potential problems. Interlocks prevent the mill from operating with the access door open, ensuring that operators do not come into contact with moving parts during operation and cause unnecessary damage.
Emergency stop system:
Emergency stop buttons and systems are strategically placed on the mill to allow operators to shut down the machine as quickly as possible in the event of an emergency or abnormal condition being detected. In this way, losses can be minimized in the event of an unexpected situation.
Access door with safety lock:
The hammer crusher's access door is designed with a safety lock to prevent accidental opening during operation. This feature ensures that the operator cannot access the inside of the mill while the mill is running.
Rotor balancing and maintenance platform:
Balanced rotors reduce vibration, contributing to more stable and safer operation. In addition, some hammer mills are equipped with maintenance platforms that provide safe access to critical components, minimizing the risk of falls or injuries during routine maintenance.
Dust control system:
To address dust and particulate emission issues, hammer mills are equipped with dust control systems including suction fans and filters. These systems help maintain air quality in the work environment and reduce the risk of respiratory problems.
Jam detection and automatic reversing mechanism:
Advanced hammer mills use sensors to detect clogging or clogging of material. In response, an automatic reversal mechanism can be activated to clear the obstruction and prevent the sudden release of stored energy.
Advanced monitoring and control systems:
Integrated monitoring and control systems provide real-time data on critical parameters, allowing operators to track mill performance and resolve potential issues promptly. This improves overall safety and operational efficiency.
Training and Education Programs:
In addition to equipment functionality, manufacturers are placing increasing emphasis on training and education programs for operators and maintenance personnel. Proper training ensures that individuals understand potential hazards and have the ability to safely operate and maintain equipment.
Challenges and future directions
Although significant progress has been made in enhancing the safety features of hammer mills, challenges remain. The variety of applications and materials processed by hammer mills requires a nuanced safety approach. Future developments may include:
Integration of Artificial Intelligence (AI):
Artificial intelligence technology can be used to analyze data from sensors and predict potential issues before they escalate, allowing for proactive security measures.
Improved material handling system:
Innovations in material handling systems can further reduce the risk of manual intervention and improve overall safety.
Global safety standards:
Developing global safety standards specifically for hammer crushers can ensure consistency and high safety levels across the industry.
Collaboration among stakeholders:
Ongoing collaboration between device manufacturers, regulators and end users is critical to identifying emerging safety challenges and developing effective solutions.
The introduction of improved safety features in hammer mills demonstrates our commitment to creating a safer working environment for those involved in the crushing process. From advanced sensors and emergency stop systems to dust control measures, these innovations are designed to mitigate common safety issues associated with hammer mills.