A cement manufacturing plant is an industrial facility that produces cement, a key binding material used in various construction applications, such as concrete, mortar, and stucco. Cement is primarily made from a combination of limestone, clay, and other raw materials, which are processed through a series of steps to create a fine powder.
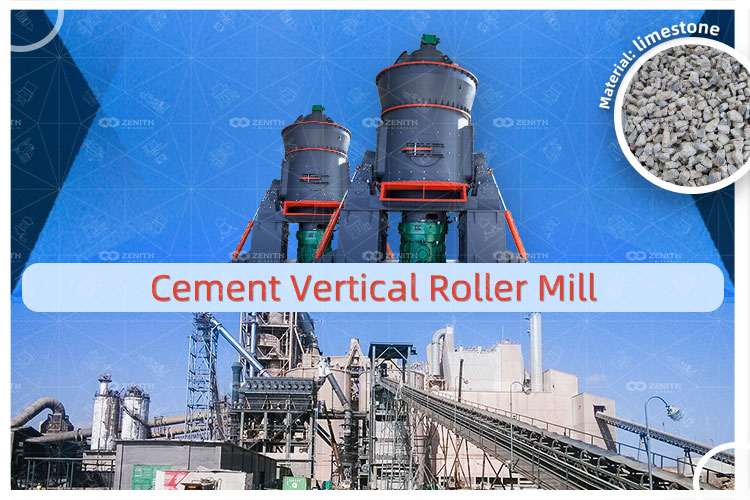
The cement manufacturing process typically involves the following stages:
- 1. Mining and quarrying: Raw materials like limestone, clay, and shale are extracted from their natural sources.
- 2. Crushing and pre-homogenizing: The extracted raw materials are crushed into smaller pieces and mixed to achieve uniform chemical composition.
- 3. Raw material grinding: The crushed raw materials are ground into a fine powder, called raw meal, using grinding equipment like ball mills or vertical roller mills.
- 4. Pyroprocessing: The raw meal is heated in a rotary kiln at high temperatures (around 1450°C) to form clinker, a semi-finished product consisting of small, nodular lumps.
- 5. Clinker cooling and storage: The hot clinker is cooled and stored in silos, awaiting the next step in the process.
- 6. Clinker grinding: The clinker is ground into a fine powder, with the addition of gypsum to control the setting time of the cement.
- 7. Cement storage and packaging: The finished cement is stored in silos and then packed in bags or shipped in bulk to customers.
A cement vertical roller mill (VRM) is a type of grinding equipment commonly used in cement plants for raw material grinding and cement grinding. It is an energy-efficient alternative to traditional ball mills, as it utilizes rollers to grind and crush the materials between a rotating grinding table and a set of rollers mounted on a vertical axis. Our company has two types of vertical roller mills, including LM Vertical Roller Mill and LUM Ultrafine Vertical Mill, both of which have a wide range of applications.
The main advantages of using a cement vertical roller mill include:
- 1. Energy efficiency: VRMs consume less energy compared to ball mills, as they require less power for grinding and have a lower table speed.
- 2. Compact design: VRMs have a smaller footprint compared to ball mills, making them ideal for space-constrained sites or retrofitting existing plants.
- 3. Higher product quality: VRMs produce a more uniform particle size distribution, resulting in a higher quality cement product.
- 4. Reduced wear: The grinding mechanism in VRMs reduces the contact between the grinding elements, leading to lower wear rates and longer operational life.
- 5. Ease of maintenance: VRMs have fewer moving parts compared to ball mills, simplifying maintenance and reducing downtime.
Overall, cement vertical roller mills are an integral part of modern cement manufacturing plants, offering energy efficiency and high-quality cement production.