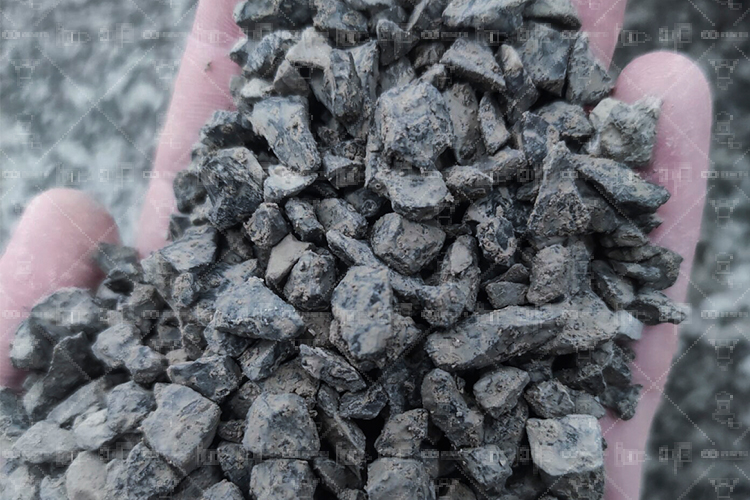
In the construction of asphalt pavement, the mixing and heating of asphalt materials is an important part, and its operating cost accounts for an important share of the entire production and operating cost. The fuel cost is relatively large, often in the millions or tens of millions of yuan. The traditional asphalt mixing plant that uses heavy oil as fuel produces significant pollution after combustion, incomplete combustion, and unstable quality. The use of clean coal powder as fuel has many advantages: low production cost, convenient ignition method, sufficient combustion, safety and energy saving, green environmental protection, and is non corrosive, harmless to equipment, safe and pollution-free storage, good stability, especially suitable for work and continuous production.
Industrial application of clean coal powder
1. In the field of coal-fired industrial boilers, it can be used as a fuel for boilers to improve their thermal efficiency, reduce pollutant emissions during the coal combustion process, and lower the cost of coal combustion.
2. In the field of metallurgical lime, lime kilns usually require high temperatures to calcine limestone. Clean coal powder, as a fuel treated by special processes, can achieve a high burn off rate during combustion and reduce energy waste.
3. Preparation of coal powder by blast furnace injection. The blast furnace injection coal powder system has a very wide range of applications in the power, steel, and metallurgical industries. The use of clean coal powder can effectively reduce carbon dioxide emissions and the generation of other harmful gases during blast furnace injection, achieving cleaner and low-carbon industrial production.
4. Clean coal powder plays a key role in the production of coal to oil and coal to chemicals in the fields of coal chemical industry and coal based new materials. By using technologies such as high-temperature gasification, coal is converted into liquid fuel or chemicals, achieving efficient utilization of coal resources.
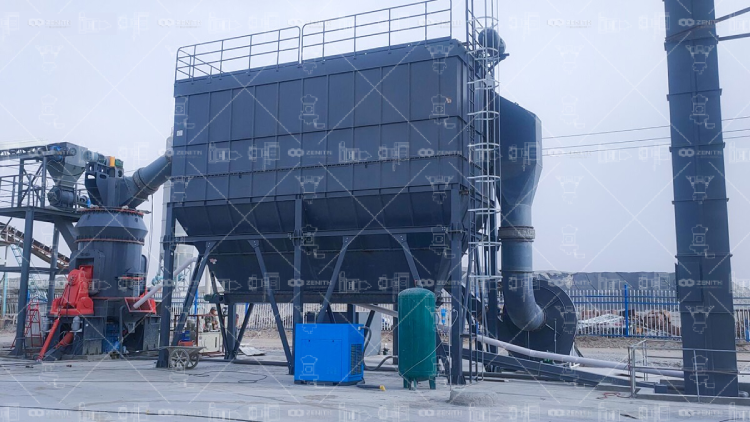
Equipment selection and production process
The fuel powder production line of asphalt mixing plant cannot do without the assistance of coal mills. Shanghai Zenith can provide professional, efficient, environmentally friendly and clean coal powder preparation. The entire coal powder production line is designed and developed by Shanghai Zenith from the front end feeding to the back end discharging. The entire production site layout is compact, well-designed, simple, clean, green and environmentally friendly, achieving standardization, large-scale and intelligence. This series of products integrates crushing, grinding, drying, and graded conveying, and achieves a one-step milling process of grinding and drying while combining drying and powder production. The large-scale grinding equipment condenses stable technological elements, equipped with a "five level safety explosion-proof system" such as CO-O2 online analysis, grinding roller hydraulic device, and automation control system, making the entire grinding process clean, environmentally friendly, safe, efficient, intelligent, and high-yield. Users can make diversified choices according to production volume, fineness, investment, and other requirements.
Production process: Raw coal is sieved through a grid screen from the raw coal yard and then falls onto a large angle belt conveyor or hoist. After being removed by an electromagnetic iron remover, the belt conveyor or hoist sends the raw coal into the raw coal bin for storage. After the powder milling system has been started, open the rod valve at the bottom of the raw coal bin, start the sealed metering belt coal feeder, and the raw coal enters the LM vertical coal mill for drying and grinding. The hot air or exhaust gas from the hot blast stove is drawn by the system fan and enters the vertical coal mill. After sufficient heat exchange with the ground coal in the mill, it carries the coal powder for sorting at the separator. The coarse coal powder with unqualified fineness falls back onto the grinding disc for grinding. The qualified coal powder enters the explosion-proof gas box pulse dust collector with the airflow and is collected. It is discharged into the coal powder bin through the sorting wheel. The impurities in the raw coal, such as some coal gangue and metal blocks, are removed from the mill through the air ring and slag outlet. Throughout the entire process, a CO-O2 online analysis system is installed. When processing coal with high volatile content, safety measures such as nitrogen protection and CO2 automatic fire extinguishing system can be set up.
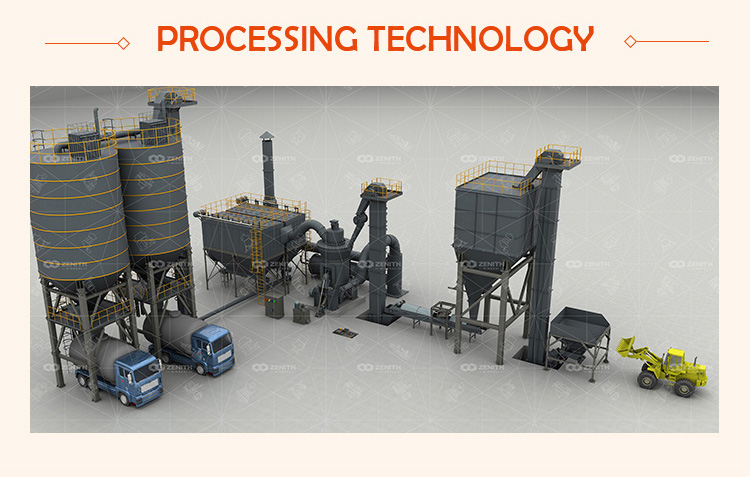
Technical advantages of LM series vertical coal mill
1. Leading technology, low investment cost, integrating crushing, grinding, drying, powder selection, and transportation, compact layout, and can be arranged outdoors, with low investment costs;
2. The operating system is safe and reliable, equipped with CO-O ₂ online detection, CO ₂ automatic fire extinguishing system and other safety and explosion prevention measures, designed to be safe and reliable, in compliance with national and industry parameter specifications;
3. High grinding efficiency, good product quality, special grinding roller and disc structure design, and the grinding roller adopts hydraulic automatic pressure device, with a large grinding area, high grinding efficiency, and large output;
4. With high drying capacity, hot air can be used to transport materials. The inlet air temperature is controlled according to the moisture content of the material. For materials with a moisture content of up to 15% in the drying process, the moisture content in the drying process is less than 1%;
5. Low operating cost: The grinding roller bearing adopts forced thin oil lubrication and is equipped with a hydraulic roller flipping device. During maintenance, the grinding roller can be flipped out of the machine by the hydraulic device. The maintenance space is large, the maintenance is convenient, and the operating cost is low;
6. A professional technical service team for integrated comprehensive solutions, providing users with design, supply, and installation general contracting services. The integrated comprehensive solution is worry free and labor-saving.