Coal-based activated carbon preparation process
Coal-based activated carbon is produced through a series of processes including grinding coal, forming, carbonization, cooling, activation, and washing. The quality of the coal powder plays a crucial role in the preparation of activated carbon. During the preparation process, it is essential to strictly control indicators such as carbon content, ash content, volatile matter, moisture, and uniformity of the coal powder to ensure the production of high-quality activated carbon products.
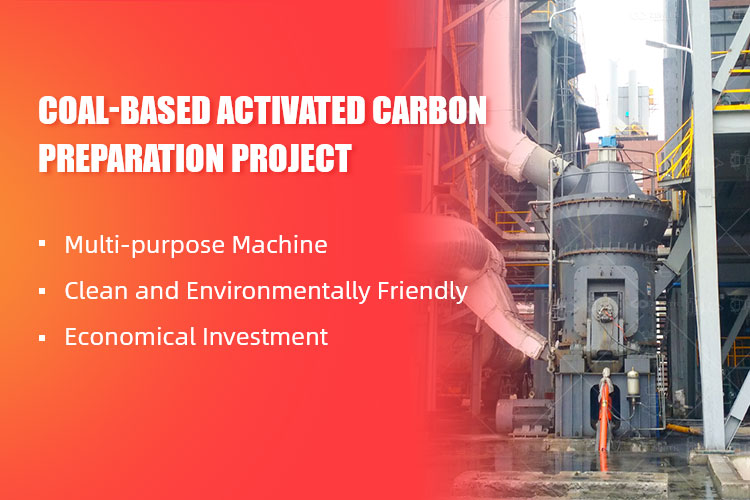
Customer Background
The customer company is a high-tech enterprise primarily engaged in the research and development, production, sales, application, and regeneration of activated carbon products, with an annual output of 50,000 tons of various high-quality activated carbons, including coal-based briquette carbon, raw coal crushed carbon, anthracite columnar carbon, and coal-based powdered carbon.
Advanced production technology will play a significant role in enhancing the quality of activated carbon and leading its upgrade and transformation, while also providing strong support for the sustainable development of activated carbon.
Material: Anthracite
Application: Activated Carbon
Equipment: Shanghai ZENITH LM Vertical Mill
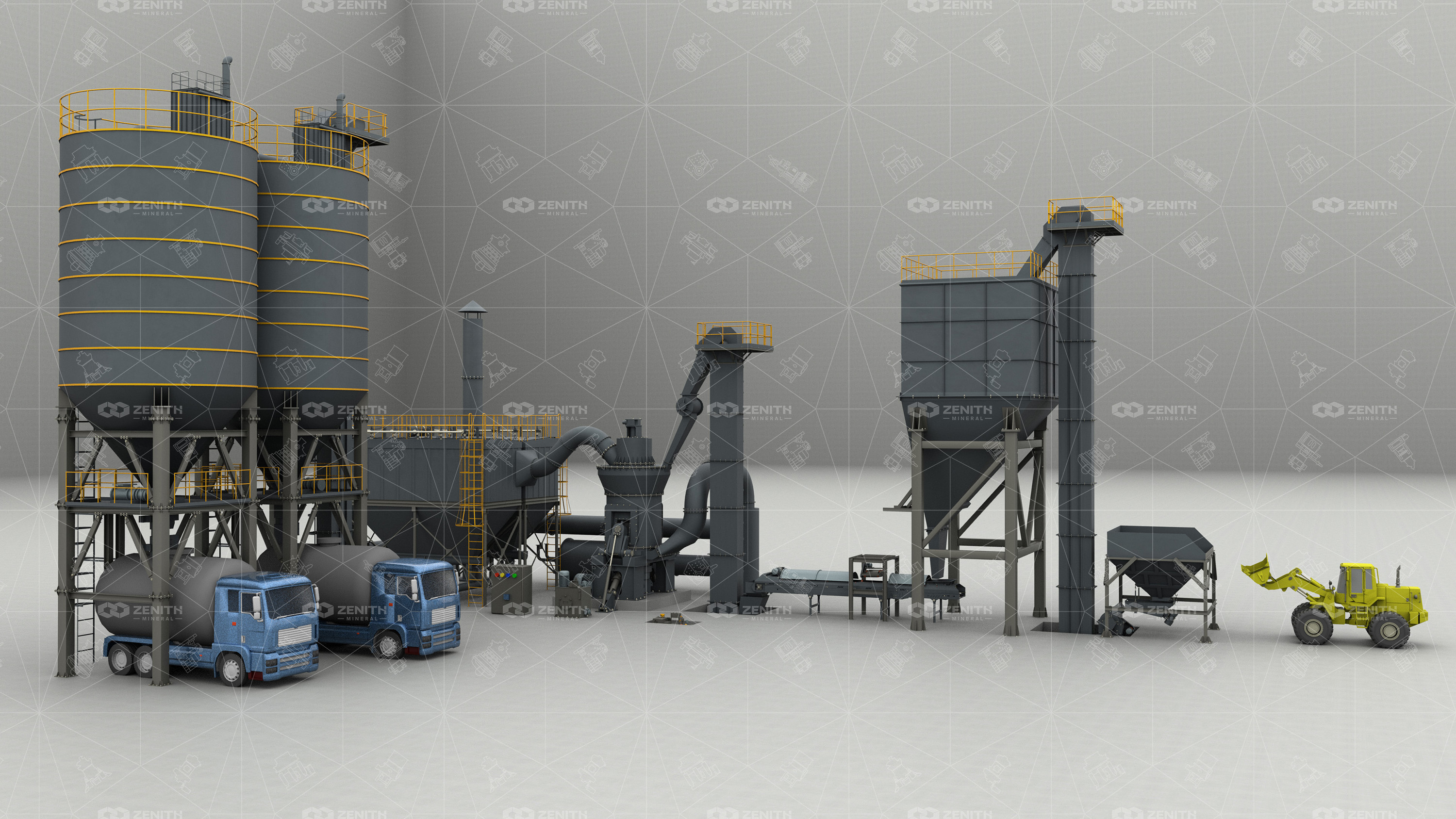
Grinding coal, as one of the important steps in production, directly affects the quality of the activated carbon product. Therefore, having a good grinding equipment is particularly important. Shanghai ZENITH has designed and manufactured the LM Vertical Mill based on years of industry experience.
The LM Vertical Mill integrates multiple functions, including crushing, drying, grinding, classification, and conveying, allowing for a wider range of fineness adjustment, thereby improving production efficiency and product quality.
Highlights of the LM Vertical Mill
- Versatile and Cost-Effective
Integrates crushing, grinding, drying, classification, and conveying into one unit, occupying approximately 50% of the area of a ball mill system, and can be arranged outdoors, offering high investment cost-effectiveness.
- Special Roller and Disc Design for High Product Quality
The unique structure design of the roller and disc ensures high grinding efficiency; the product has a uniform particle size distribution, good quality, excellent flowability, and high activity.
- High Degree of Automation, Saving Labor
Equipped with an automatic control system, it allows for remote operation, interlocking protection, reliable operation, and easy handling, significantly reducing labor costs.
- Thin Oil Lubrication for Easy Maintenance
The grinding rollers use forced thin oil lubrication and are equipped with a hydraulic roller turning device, allowing the rollers to be turned out of the machine for maintenance without disassembly, making it convenient and quick.
- Hot Air Drying with Strong Adaptability
Hot air can be used to transport materials, drying materials with moisture content up to 15% before grinding, with the output moisture content being less than 1%.
- Clean and Environmentally Friendly, Compliant with National Standards
The system is fully sealed and operates under negative pressure, preventing dust overflow; the equipment has low vibration and noise levels, making production operations more environmentally friendly.