Analysis of four causes of vertical mill vibration and detailed analysis of treatment measures
The internal structure of the vertical mill is compact, and there are fewer external equipment, which can save a lot of space and reduce initial investment. Vertical mills also have the advantages of low dust emission, low noise, and low environmental pollution, making them widely used in powder grinding production.
Under normal circumstances, the vertical mill operates smoothly and the noise level does not exceed 90 decibels. However, if not operated properly, it can cause vibration and generate significant noise. For a vertical mill, reasonable vibration is allowed to exist, but if the vibration is too large, it will inevitably cause damage to some accessories in the vertical mill. Therefore, strict control of the vibration of the vertical mill is necessary in the production process.
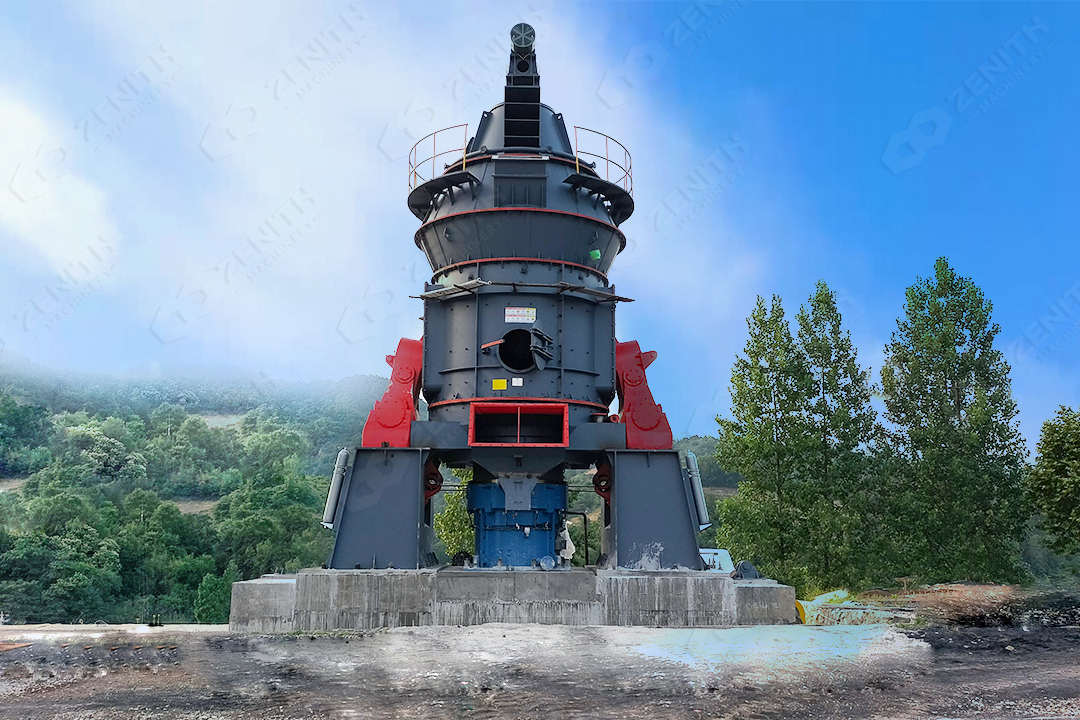
Analysis of the causes of vertical mill vibration
In actual production operations, many vibrations are caused by improper operation, such as vibrations caused by unstable material layer control. Due to the thin material layer, there will be very few materials that can be ground, resulting in a decrease in grinding output. At the same time, if the material layer is too thin, it can also cause rigid contact between the grinding disc and the grinding roller, which can cause significant vibration, leading to severe wear of the vertical grinding equipment and increased energy consumption. If the material layer is too thick, the grinding ability of the vertical mill will be reduced, and the internal circulation load will increase, causing the up and down jumping of the grinding roller, which will cause serious damage to the equipment and affect its safe use. Therefore, the control of the material layer is very important, and there are many reasons that affect the change of the material layer. Among them, the material characteristics include the moisture content of the material, friction factor, and the particle size of the material entering the grinding, as well as the influence of factors such as temperature and pressure difference.
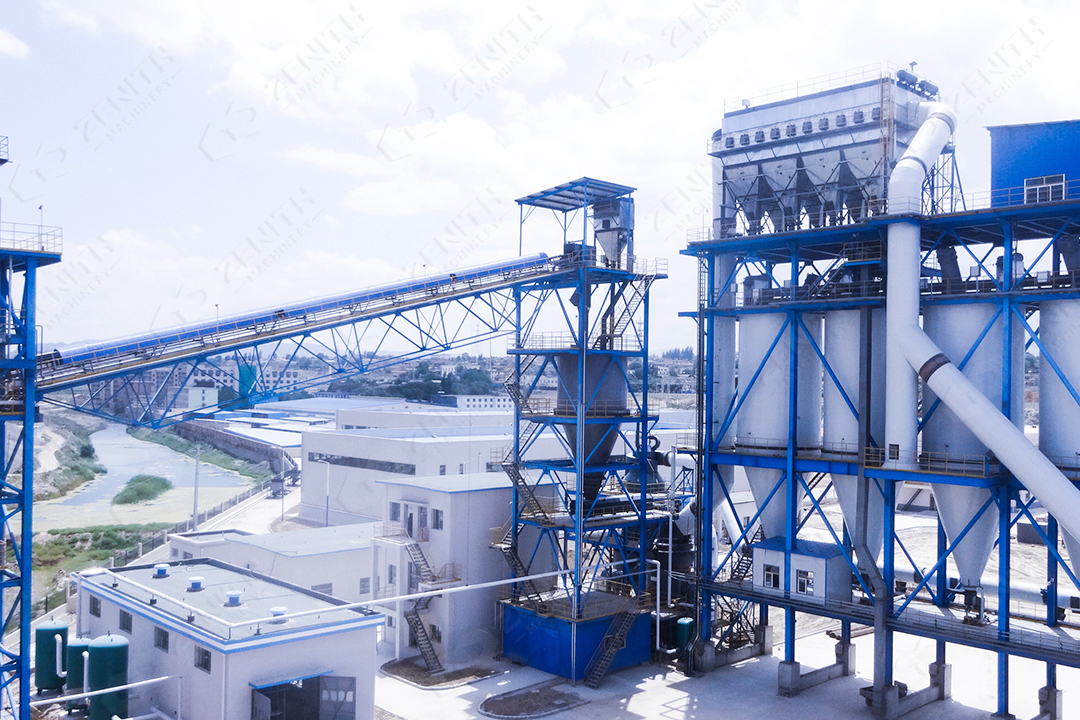
Material characteristics
Material friction factor: directly reflects the magnitude of internal friction generated during the grinding of various materials. It directly affects whether the material layer can form a stable abrasive layer thickness, and whether the stable material layer thickness can be maintained directly affects the degree of vertical grinding. Materials with low friction factors will be squeezed out of the groove due to the squeezing effect, inevitably causing the material layer to be too thin, which can easily lead to direct contact between the grinding disc and rollers, causing equipment vibration and damage to internal equipment; If the friction factor is large, the material will be subjected to very small crushing and form a cake shape, which is difficult to loosen and causes grinding difficulties.
The particle size of the material entering the grinding disc: The particle size of the material entering the grinding disc should match the grinding roller and grinding disc. As the diameter of the grinding roller increases, the peripheral velocity of the grinding roller also increases, resulting in an increase in frictional force. Therefore, the grinding roller is more easily engaged with the material, and the material being ground is more easily crushed into a material layer. Therefore, the particle size of the material entering the grinding can be appropriately increased. But when the material particles are too large, it will cause the grinding roller to be greatly impacted, resulting in vibration caused by the imbalance of the three rollers; Due to the small particle size of the material, it will enter the powder selection machine with the hot air fan and cannot form a material layer on the grinding disc, causing direct contact between the grinding disc and the grinding roller to generate vibration. Generally speaking, the particle size entering the vertical mill should be around 5% of the diameter of the grinding roller, which is the best.
Material moisture content: The amount of moisture in the material has a significant impact on the grinding process. If the moisture content is too high, the material is not easy to dry. Grinding materials that are too wet can wrap around and adhere to other materials, even wrap around the grinding roller, causing material accumulation on the grinding disc, making it difficult for the grinding roller to press down, and causing vibration to jump and stop. If the moisture content of the material is too low, the viscosity of the material will be too low, and the friction factor between materials will decrease, making it difficult for it to stay on the grinding disc for a long enough time and form a certain thickness of material layer. This will cause rigid contact between the grinding disc and the grinding roller, exacerbating vibration.
The difference between the inlet and outlet grinding pressures
The difference between the inlet and outlet pressures is called the pressure difference, which is one of the main reasons affecting the vibration of the vertical mill. The change in pressure difference directly reflects the change in the internal circulation load rate of the vertical mill, which is related to many factors such as material particle size, material characteristics, grinding pressure, ventilation inside the mill, material moisture, and feed rate of the mill. For example, if the material is fed into the grinding particles too small, the grinding pressure is high, the moisture content is low, the feeding amount is large, and the ventilation is insufficient, it will cause an increase in differential pressure and thickening of the material layer; On the contrary, it will lead to a decrease in differential pressure, thinning of the material layer, causing vertical mill vibration. Failure to adjust in time will cause vertical mill jumping and stopping.
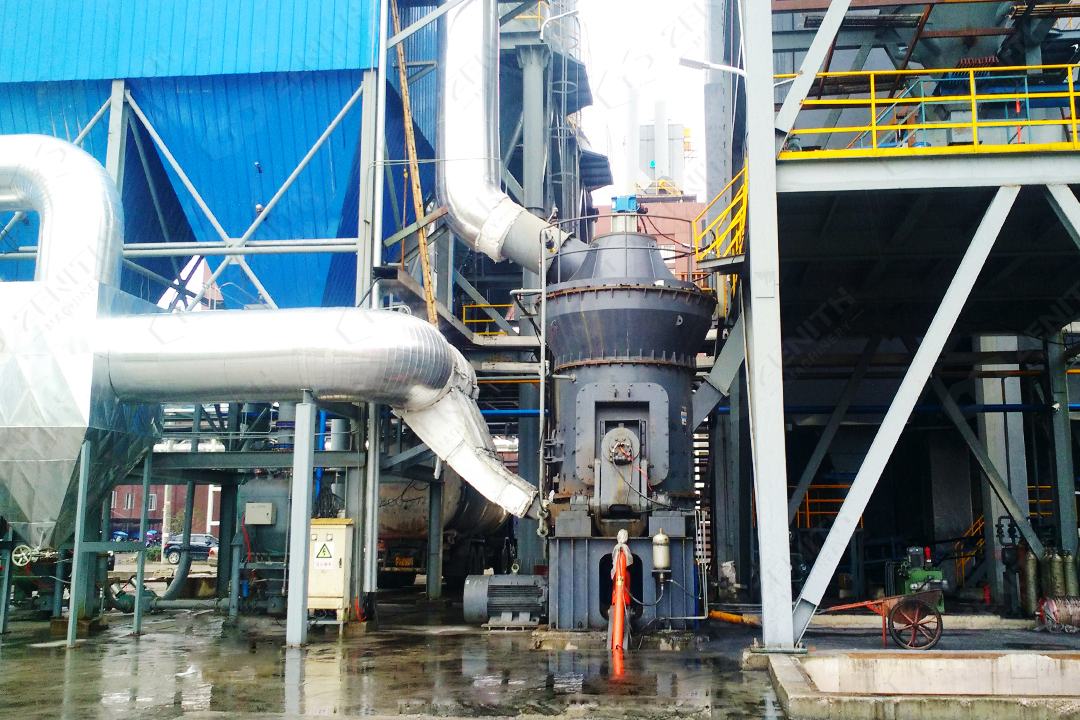
The temperature of the hot air
The temperature of the hot air has a significant impact on the vibration of the vertical mill, as the ventilation rate in a fixed vertical mill needs to ensure the drying efficiency of the materials. Therefore, it is necessary to control the temperature of the hot air entering the mill, which is mainly based on the moisture content of the materials entering and exiting the mill. However, poor air temperature control can also affect the grinding efficiency of the vertical mill to a certain extent. If the air temperature is too high, it can achieve good drying and grinding effects, but it can cause the material layer to be too thin. If the wind temperature is too low, it will cause difficulties in drying the materials, making it difficult to carry out grinding, and the materials are easily compressed into cakes, causing vibration in the vertical mill.
In general, the wind temperature at the inlet should be between 200 ℃ and 250 ℃, while at the outlet, the temperature should be controlled between 80 ℃ and 120 ℃ based on the moisture content of the material and the water spray inside the mill. Under this parameter, the vertical mill operates smoothly and efficiently without generating significant vibrations.
Grinding pressure
Grinding pressure is the total pressure exerted by the center frame, hydraulic system, and the weight of the grinding roller. Grinding pressure is directly related to the compression ratio of the material and the thickness of the material layer. As the grinding pressure increases, the thickness becomes thinner; On the contrary, the pressure decreases and the thickness increases.
Countermeasures for controlling vertical mill vibration
Feeding operation
When the moisture content of the material is high, the outlet temperature should be appropriately increased to increase the pressure difference inside the mill to the ideal value. If there is insufficient feeding and insufficient return, the feeding should be increased to ensure normal pressure difference inside the mill, in order to avoid vibration. If the material layer is too thick, the feeding amount should be reduced in a timely manner and the discharge port should be ensured to be unobstructed; On the contrary, it is necessary to increase the feeding amount.
Grinding pressure control
If the feedback value of the grinding pressure of the vertical mill is less than the set value, it indicates that the accumulator pressure is too low and nitrogen must be replenished in a timely manner.
temperature control
If the temperature is too high, it can be adjusted appropriately by adjusting the power of the grinding machine or directly opening the cold air valve.
Differential pressure control
When the feeding amount is large and the grinding capacity is insufficient, it will cause an increase in the pressure difference inside the mill. At this time, the feeding amount should be appropriately reduced according to the power of the mill. If the product is too fine, it will increase the internal circulating load, causing an increase in pressure difference and vibration. Therefore, it is necessary to appropriately reduce the speed of the powder selection machine.
In the actual production process, we need to combine specific situations to carry out appropriate operations on the vertical mill. In addition to summarizing the above reasons, it is also necessary to strengthen equipment maintenance and safety inspections in production to ensure a stable and safe operating environment for the vertical mill.